There’s no better feeling than getting a fresh bat and I’m sure that everyone out there remembers the day that they got their very first baseball bat.
There’s something incredibly exciting about a new bat that’s incredibly hard to explain – you know what it is, I know what it is, every baseball fanatic out there knows what it is and it’s the reason that we love the game so much, but it’s a magical feeling that we can’t quite put into words.
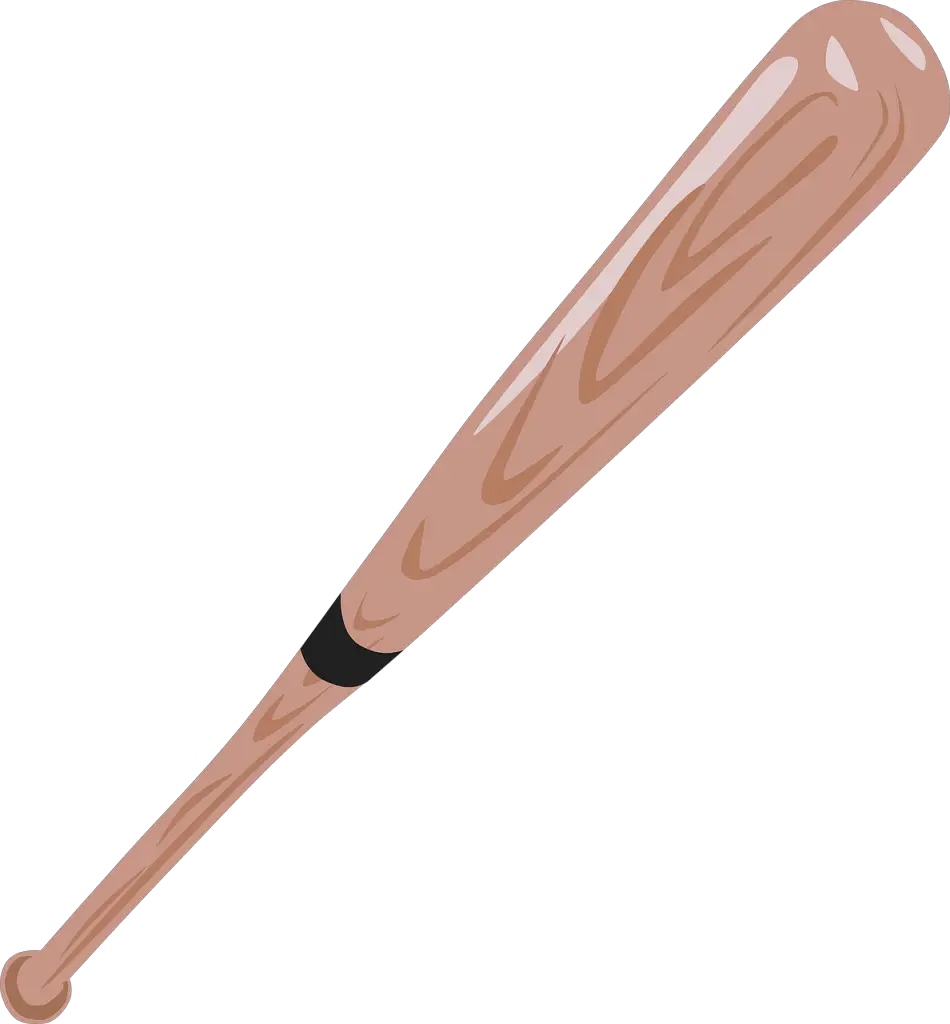
But, did you ever stop to think about where that magic comes from and the process that went into creating that awesome feeling you feel when you buy a new bat and hold it in your hands for the first time as you step up to practice with your tee and net?
No matter what type of baseball bat you favor, whether an old-school wooden bat or a more modern metal bat, there’s a really interesting process that goes into the manufacturing.
In this article, we’re going to take a look at those very processes to try and gain a better understanding of where that new bat feeling comes from.
How Wood Baseball Bats Are Made
There’s a range of wood bats out there on the market and that are used by both the pro’s and those just starting to learn the mechanics of hitting. Let’s take a look at the steps of the wood bat manufacturing process.
Step #1) Source the wood
There’s a lot that goes into making a wood bat, but the most important part of the process is finding the perfect piece of wood.
All of the best bat manufacturers have partnerships with mills in the US and Canada who provide them with the highest quality grains of beech, ash, maple, and birch.
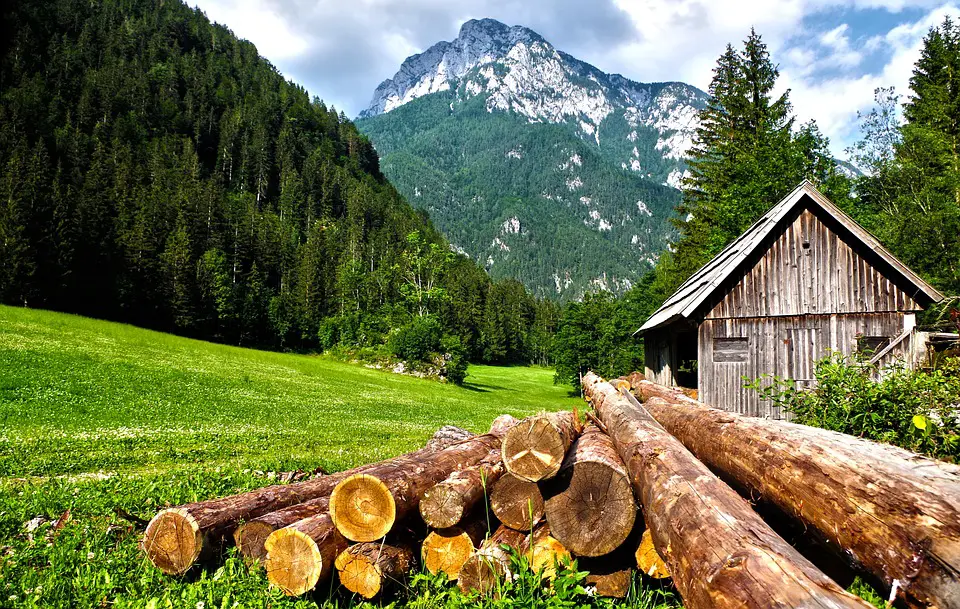
More often than not, the wood is not only harvested but cut into the appropriate shape at the mill.
Firstly the wood must be cut into long rectangles then dowelled into a cylindrical shape before being dried and shipped out to the manufacturer.
Step #2) Shaping the bat
There are people out there shaping their bats by hand, but for mass production, bats are shaped using CAD (computer-aided design).
The template specifications are drawn up using computer software which can then be exported a CNC lathe which shapes the wood into the specific bat shape in minutes.
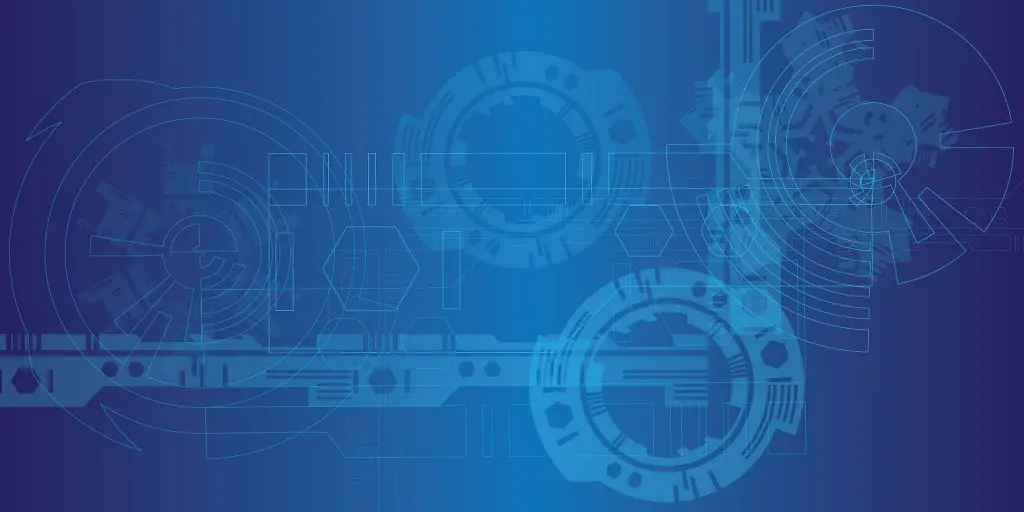
Once the lathe has shaped the bat it has to be checked for imperfections.
These can come in the form of splits, knots or any general blemishes in the wood.
Any cast-offs, or ‘blems’ can still be used and sold at discounted rates as these imperfections will affect the overall quality and lifespan of the bat.
Step #3) Sanding
This is a key part of the process.
Bats must undergo a series of sanding cycles with different grades of sanding paper in order to give it the smoothest finish possible.
Sanding is also crucial to the overall comfort when gripping the bat.

Step #4) Finishing
After the cutting, shaping, and sanding, you’re left with a bat ready for customization so the finishing part of the process is where the manufacturer can really get creative.
Now the bat can have any kind of color or unique design placed on it before the wood is stained and sealed to increase its strength and durability.
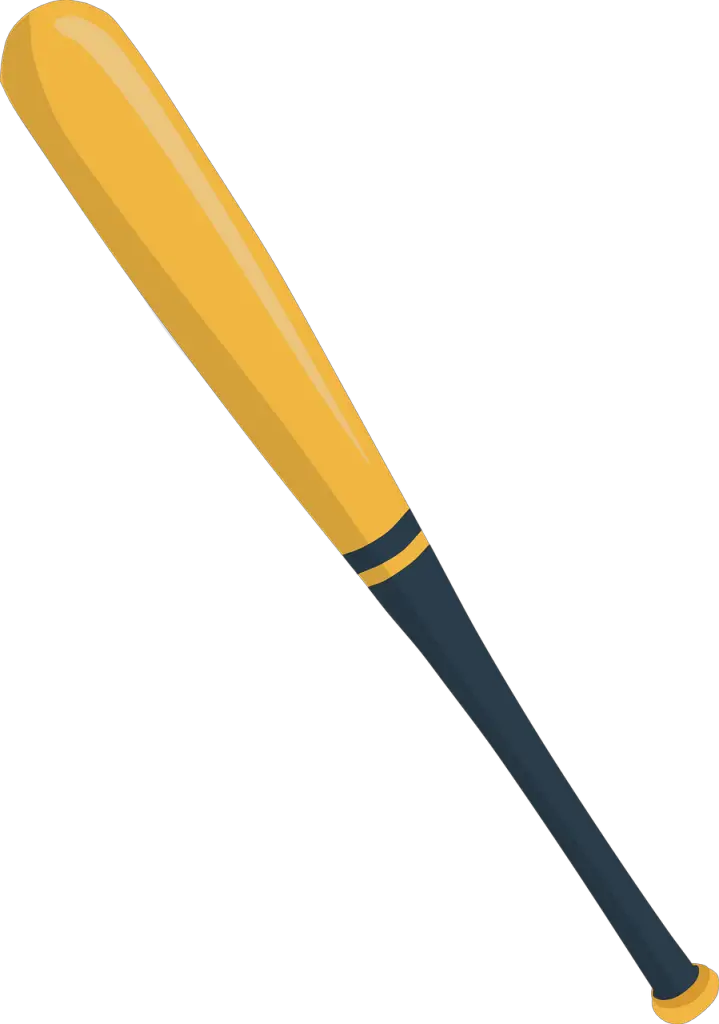
From here, some custom bats go on to be engraved and personalized with specific text or logos.
Maple vs Ash vs Birch
Choosing the type of wood for your bat isn’t easy and something which requires a little research so that you can get the most out of your bat.
The most common types of wood bat are made from either maple, ash or birch and we’re going to take a look at each type to help you in your choice.
Maple
Often the choice of pro’s,
Maple is a highly dense wood which means it’s going to really hold its own against high-velocity pitches and stand the test of time.
A denser wood will also give the bat more pop.
Now it’s time to get a bit more technical. Maple is what’s known as a diffuse-porous wood. This means that:
- a) it will not splinter and…
- b) the more impacts it receives, the denser it will become.
A major downside to maple is that it’s more susceptible to humidity than other wood types and in a humid climate, the wood will suck up moisture and get heavier.
Ash
Ash is a traditional material for wood bats and has been used for a long time by manufacturers.
One key feature of ash is that it has more flexibility when compared to maple.
This means that bats made from ash are easier to whip and generate speed in the hit.
As an open-grain wood, ash is constantly drying out and an ash bat will not always maintain its already low moisture content throughout its life.
A negative side effect of this is that ash is more likely to splinter than other wood bats deeming them less durable than maple.
Birch
Bats made from birch are lighter and offer more flex than other wood types.
Birch is a softwood so it can be easily swung at high velocities.
The main drawback to birch is that it just isn’t as strong as maple and the surface of birch bats will often dent on the first impacts.
A softer surface also reduces the power output of the bat, especially when compared with maple.
How Aluminum Baseball Bats Are Made
If you prefer the ‘ping’ of an aluminum bat when you hit the ball to the ‘snap’ of wood, then this section is for you.
Let’s see what goes into creating the perfect aluminum baseball bat.
Shaping
The process begins with aircraft-grade aluminum rods which are cut to short lengths known as blanks.
As with wood bats, these blanks then go through a CNC lathe which drills a tunnel into the center of the blank.
Next is the tapering of the blank.
This is done with a 300-tonne weight which inserts a shaping tool into the tunnel to stretch and taper the blank into a more familiar, bat-like shape.
After being cleaned, the blank is stretched again, this time using a 400-tonne weight.
This machine is the one that gives the bat its full shape and length.
Once the blank has its lengthier shape, it needs to be tested for alignment. This is done using a number of gauging tools.
Any imperfections can be adjusted to ensure the bat is straight.
From here, the bat enters another lathe.
This one is designed to cut the bat to its final length and thread the inner edge of the tip for attaching the bat’s cap. Similarly, the handle is trimmed to size with a saw.
Sanding
Now the bat is to shape and size it needs to be smoothed down in order for comfort, aerodynamics, and for the paint to stick to the metal’s surface.
The bat is machine sanded to achieve ultimate smoothness.
Painting & finishing
Heavy-duty spray paint is used to give the bat its final color.
This paint is also weatherproof to ensure the bat won’t get damaged by the elements over time.
Once painted, the trademark information and any other aesthetic decorative features can be added.
Finally, the bat is sprayed with a layer of polyurethane for an added layer of protection and the plastic end cap is fitted.
How Composite Baseball Bats Are Made
A composite bat is a bat that is either part reinforced or completely made from a strong carbon fiber polymer known as a composite.
Carbon fiber bats have a bit more elasticity than other bats and are a great tool to improve your hitting. Here’s how they’re made.
Shaping
These bats start out as sheets of carbon fiber imbued with a resin.
These sheets are melted together using a heated iron to create a layered stack of carbon fiber.
From here, the layers are sent through a high-pressure steel roller to fuse the layers together and flatten them out.
From here, the pressed carbon fiber layers are cut into large square sheets which will be used to create the shape of the bat.
This is done by rolling the sheet around a metal bat template. Once the sheets are wrapped around the template a layer of polypropylene tape is wound around it to remove any air.
The next stage of the shaping involves a large industrial oven in which the carbon fiber is baked for two hours to cure it and ensure the resin and the carbon fiber molecules fuse together.
After baking, the outer layer of tape is removed and a sheath of carbon fiberglass is added and secured with tape.
Another layer of thick carbon is then added and taped to the bat form. From here it goes into a mold and has an epoxy resin injected and heated to create a solid carbon bat
Now another machine is used to extract the template that was originally used to shape the carbon fiber sheets right at the beginning of the process.
Testing
Now the bat has its form it needs to be tested to ensure its precision, strength and flexibility. A variety of tests are done using specially designed calibration equipment.
Sanding
The next stage of manufacturing involves another lathe that spins the bat at speed against a sanding tool to ensure complete smoothness across the whole of the bat’s surface.
Finishing
Straight from the lathe, the bat gets dipped in black primer and hung up to dry.
Once dry, the bat can be painted and decorated to the specification of the design.
Finally, plastic caps are added and the bats are weighed to make sure that they meet governing body specifications.
Wood vs Aluminum vs Composite
This is a classic debate within the baseball world. Which bat is the best?
Wood, aluminum, or composite.
A lot of it comes down to the level you’re playing, your style, sometimes your batting stance, and your budget. Let’s take a look at the pros and cons of each bat type.
Wood Bats
Wood bats are generally used by top-level players. This is for a number of reasons.
Firstly, they require much more skill to use and it’s a professional tradition to use a wooden bat.
Secondly, the MLB chooses wood as it is a safer bet type when being swung at such high speeds.
Pros
- Usually less expensive than other bat types
- Different types of wood available to choose from
- Used by the pros – generally, wood bats provide better swing mechanics and feel.
- More choice for customization in terms of weight, style, and length.
Cons
- More difficult to use so not a great choice for youth players.
- Wood bats may splinter and have a shorter life span.
- Heavier than other bat types.
Aluminum Bats
Aluminum bats can be used at all levels outside of professional leagues so they’re great for younger players and players in college and high school leagues as they are generally considered to be easier to use than wood bats.
Pros
- Usually less expensive than composite bats.
- Good for cold weather.
- More lightweight so easier to swing and generate speed.
- Don’t break as easily as wood bats.
- A large sweet spot makes them easier to use.
Cons
- Aluminum bats tend to dent.
- Not as effective as wood bats at a higher level.
- Generally heavier than composites.
Composite Bats
Composite bats are the lightest type of bat making them perfect for younger players.
They also vibrate less on impact and have a more balanced swing weight so really they’re the choice for anyone outside the professional leagues looking for comfort.
Pros
- Composite bats generally have a lower swing weight than wood and aluminum bats.
- Made from stronger materials.
- Good weight to strength ratio.
Cons
- They are the most expensive bat type.
- Require a break-in period.
- Over time, composite bats will crack.
Why do MLB Players Use Wooden Bats Over Aluminum?
The MLB banned the use of aluminum bats for a number of reasons that we briefly touched on in the previous section, but let’s look at it in a bit more detail.
Aluminum bats allow players to generate more exit speed and a professional armed with a metal bat could really exert a lot of force on a ball putting other players and spectators in danger.
Aside from the obvious safety reasons, baseball is a sport of fine traditions and wooden bats have always been used so it’s a case of purism and following the conventions of the institution.
Finally, there’s the fact that bats made from wood require a higher skill level to be used effectively, and to play at the top level, you need to be able to demonstrate your prowess under tougher parameters.
And let’s be honest – professional players don’t need the extra help of a bigger bat or a bat that’s easier to swing if they can already crush with a wooden bat.